After some little housekeeping items on the boiler such as chasing threads on the nozzles and cleaning weld-splatter off of hand holes, it was time to prepare for setting the tubes. Tubes were ordered from Anderson Tube in Hatfield, PA, and the tube sheets were prepared by lightly sanding the holes radially. Unlike larger boilers where a one-inch variance in tube lengths is not uncommon, all of these holes were within 0.062" of each other, so I cut all of the tubes to the same length.
Tube rolling or expansion is an art far beyond this blogspace. If you would like to read more about the technical aspects of it, click here. In short, it involves expanding the tube into the fixed space of the sheet. Engineers would say that we want to end up with the tube plastic and the sheet holes and ligaments elastic. After rolling in thousands of tubes in this brief life, there's still a certain thrill to it because it is one of those few areas left to artificers where the ideal balance between over-rolling or under-rolling is a matter of feel.
Here, we're looking at the combustion chamber or back end of the boiler, and the first eleven tubes are rolled in. The particular expander I'm using has a flaring feature, which I'll explain more about another day. The goop in the holes is Crisco and while attributing their fine product, I'm sure lubricating tube expanders is something they would not like to be associated with. But it does the job and doesn't interfere with the heat-transfer welding that comes later. In some of the holes, one can see the degree that the tube has expanded. The goop makes the transition look larger than it is - we want this transition to be gradual without sharp edges. (By the way, some measurements for you technical types: The holes were bored 1.531", the tubes are 1.50" with 0.095" wall thickness.)
I manipulated the expander by hand, using a T-handle. That way there wasn't a lot of racket and I could be in my quiet, happy place, feeling the moment of set. In addition to feel, one sign of a good tube set in sheets this thin (0.375") is just when the mill scale on the sheet right around the hole begins to split into a micro lattice. If you look at the photo, this lacing appears as a thin, lighter halo around some of the tubes. That can occur within a sixteenth of a revolution of the expander, so one has to be alert.
The next blog entry will treat flaring and beading the tubes on the front (smokebox) end, and heat-transfer welds on the back (combustion chamber) end.
Sunday, December 1, 2013
Saturday, November 16, 2013
Stress Relieved
Here's a shot of the boiler front after stress relieving. Doesn't it look more relaxed? Now on to boring two washout plug holes. The tubes were ordered yesterday. The activity in the picture foreground is the layout and design for the firedoor ring and the smokebox.
Saturday, November 9, 2013
Ready for the Oven
I remembered the camera this morning before leaving for the shop, which is better than that moment when one thinks, "This would make a nice picture." First, both sheets received their chamfer at the stay holes for the welding out of the stays. We have a special 37º bit for the Carlton drill press that makes short work of this. The stay material was cut to length and before I knew it, the back end was ready for the stress-relieving. Here's a shot of the back end. The ends of the stays that were just welded out are the three shiny buttons:
Then the boiler was flipped on its back and the stays welded in on the front. This might be a good time to explain the other things we're seeing in the photos. The lifting chain in both photos is threaded through the tube sheets. The tubes will be rolled into these holes after stress-relieving the boiler. The big nozzle at the bottom of both pictures is one of two hand holes for inspection, washing, etc. Think of it as a window into the boiler's soul. The smaller nozzle in the bottom of the picture, below, is the fitting for the boiler's blowdown. The boiler is drained through the blowdown. Crud can also be blown out the blowdown during operation. This is done to the greatest visual effect by placing the blowdown through-hull fitting on the hull just above the water line. After this second photo, I give a brief description of stress-relieving.
Welding is a fusion and metal deposition process. As such, uneven stresses can build up in the pieces being welded and in the weld itself. With a small boiler such as this one, we have the luxury of placing the whole assembly into an oven and raising the temperature for an extended period of time until about 90% of the stress is relieved. Think of it as a nice soak in the tub after working hard in your garden or shop. Not all of life may be mended, but emerging sanguine in complexion and disposition leaves one more fit to be around. The boiler feels the same way. For those who need to know, this fuller explanation from Houston Heat Treat, below:
Stress-relief operations are typically done by subjecting the parts to a temperature approximately 40- 75ºC (105-165ºF) below the Ac1 transformation temperature — about 727ºC (1340ºF) for steel. Stress relief is typically performed for carbon steel at approximately 500-650ºC (930-1200ºF). The elimination of stress is not instantaneous (that is, the process is a function of both temperature and time). To achieve the maximum benefit, some time at temperature (typically one hour per 25 mm of cross-sectional area once the part has reached temperature) is required. This removes more than 90% of the internal stresses.
And a handy diagram lifted from Wikipedia, below, shows the A1 line. Aren't steam launches an education?
Saturday, October 26, 2013
The Very Bowels
The last two Tuesdays and the last two Saturdays were spent in what I call the very bowels of this project - welding out the primary weldments of the boiler. The two tube sheets are now in, as is the furnace. The horizontal stays are the last weldment.
It is one thing to summarize; another to carry out. First, the 0.375" thick tube sheets are machined or ground for the relief bevel with @ 0.90" land. The sheet is then tack welded in place with short tacks. Then a 7018 (a low hydrogen rod) root pass is welded in. (Our shop utilizes a 7018 root pass procedure in order to avoid root cracking, a common problem with 6010 wire on circular or pipe weldments.) The root pass is almost ground out with a 4.5" grinder to ensure complete penetration and to ensure that there are no inclusions in the metal. Following passes are laid in and ground out as needed. I skipped around to minimize bowing and distortion, but it is hard to avoid.
Here is an image off the web. It is of a MIG weld but it is still illustrative. It shows a root pass, the pass ground down to eliminate inclusions and the "keyhole" at the arc, a mark of good penetration.
It is one thing to summarize; another to carry out. First, the 0.375" thick tube sheets are machined or ground for the relief bevel with @ 0.90" land. The sheet is then tack welded in place with short tacks. Then a 7018 (a low hydrogen rod) root pass is welded in. (Our shop utilizes a 7018 root pass procedure in order to avoid root cracking, a common problem with 6010 wire on circular or pipe weldments.) The root pass is almost ground out with a 4.5" grinder to ensure complete penetration and to ensure that there are no inclusions in the metal. Following passes are laid in and ground out as needed. I skipped around to minimize bowing and distortion, but it is hard to avoid.
Here is an image off the web. It is of a MIG weld but it is still illustrative. It shows a root pass, the pass ground down to eliminate inclusions and the "keyhole" at the arc, a mark of good penetration.
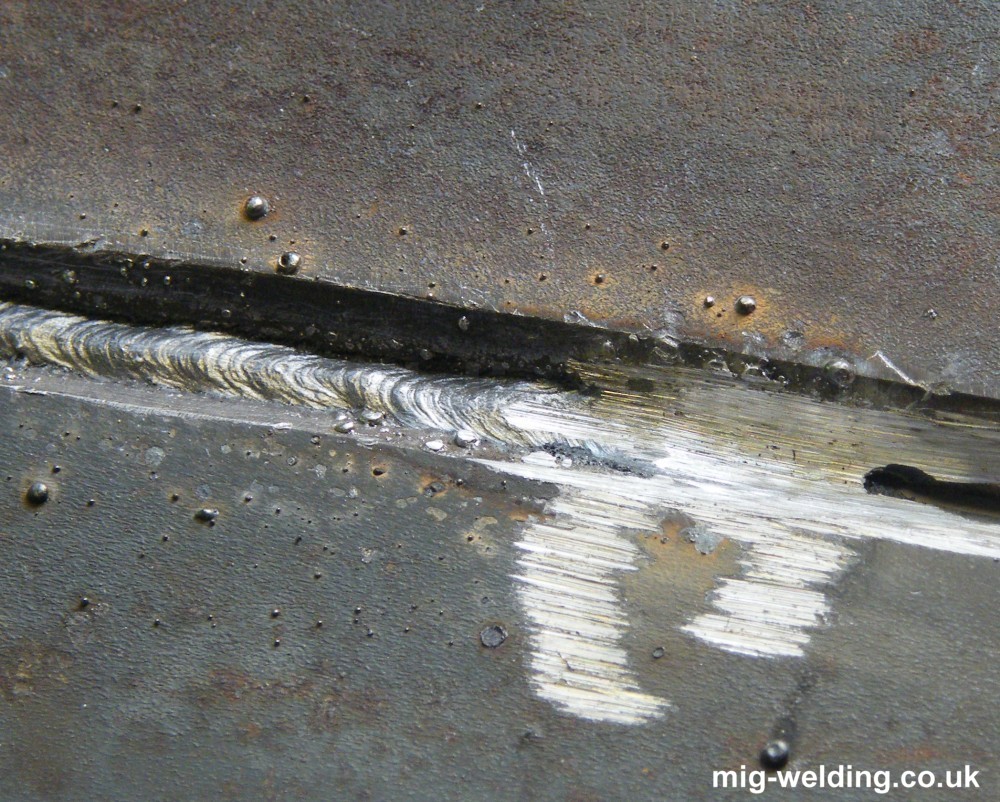
Sunday, August 4, 2013
Interior Update
A picture tells the story - so let's talk about what we see here that's new:
The deck substructure is finished except for the stern. I was getting ready to finish that substructure too - the stern king plank is in the foreground - when the rudder and steering gear called out for attention before being buried under structure. The rudder gland is mounted inboard with a piece of cutlass bearing bonded into the hull structure to guide the rudder post. One can see the guiding dowel still in place. There's a story there too. We have had as wet a summer as the cousins across the pond did last year. The dowel has swelled in the humidity, so it's there until I put some heat lamps on it ... Rudder, quadrant and cables to follow.
Beyond the "rudder post" is the removable hot well receiving a dry fit. One can see light through it because I have not yet bonded in the bottom. The hot well will sit under part of the starboard seats. It will be held in place with cleats. Disconnecting some unions and lifting it out will facilitate annual maintenance and cleaning.
The deck substructure is finished except for the stern. I was getting ready to finish that substructure too - the stern king plank is in the foreground - when the rudder and steering gear called out for attention before being buried under structure. The rudder gland is mounted inboard with a piece of cutlass bearing bonded into the hull structure to guide the rudder post. One can see the guiding dowel still in place. There's a story there too. We have had as wet a summer as the cousins across the pond did last year. The dowel has swelled in the humidity, so it's there until I put some heat lamps on it ... Rudder, quadrant and cables to follow.
Beyond the "rudder post" is the removable hot well receiving a dry fit. One can see light through it because I have not yet bonded in the bottom. The hot well will sit under part of the starboard seats. It will be held in place with cleats. Disconnecting some unions and lifting it out will facilitate annual maintenance and cleaning.
Sunday, July 7, 2013
Stemhead and Deck Structure
Finally whittled down that huge hunk of doug fir and laminate that is the inner and outer stem. Here it is prior to sealing and finish sanding. You can see where the staples were on the laminate before I pulled them.
Also a few shots of the subdeck structure and carlins. In the area just in front of the coaming, I probably went overboard with the 0.625" okoume - no pun intended - but I wanted plenty of support for this area of the deck. Notice the temporary cleats under the ply, giving the necessary camber until the epoxy sets up.
Here's a shot of the kingplank and the foremost carlin. The kingplank is laminated okoume and the carlin is poplar.
I took the following shot because it intrigued me and highlighted a number of construction details: the scarfed fir sheer and the fit and bond at station No. 2 of sheer, topsides, bulkhead and subdeck. The black of course is topsides paint that worked its way down during that process. This is the kind of stuff that will soon be obscured. It will be nice to remember what it looked like.
Also a few shots of the subdeck structure and carlins. In the area just in front of the coaming, I probably went overboard with the 0.625" okoume - no pun intended - but I wanted plenty of support for this area of the deck. Notice the temporary cleats under the ply, giving the necessary camber until the epoxy sets up.
Here's a shot of the kingplank and the foremost carlin. The kingplank is laminated okoume and the carlin is poplar.
I took the following shot because it intrigued me and highlighted a number of construction details: the scarfed fir sheer and the fit and bond at station No. 2 of sheer, topsides, bulkhead and subdeck. The black of course is topsides paint that worked its way down during that process. This is the kind of stuff that will soon be obscured. It will be nice to remember what it looked like.
Thursday, June 27, 2013
WoodenBoat Show Eve
Well, it's WoodenBoat Show Eve, when all of us trolls emerge from our shop caves to glory in our art. For my own part, I've been welding and fitting sub-deck structure since the last post - things that are not photogenic, which hopefully explains the dearth of updates.
To whet one's appetite, go here for show information. See you at the show!
To whet one's appetite, go here for show information. See you at the show!
Saturday, April 27, 2013
Boiler Erection
Here's something new. This is the shell of the boiler for the launch. The perspective is looking at the bottom of the barrel - it's a scotch marine - the coupling front and center is the blowdown. The hand hole to port is for bottom wash and clean-out. On the inside one can see the cluster of four outlets that make up the two safeties, whistle and auxiliary. The main and throttle are further forward. They'll have a drypipe fitted later. The starboard upper hand hole is for washing the tubes. Not bored yet are the feedwater inlets and the other two 1.5 wash-out holes. This is a certified build and will receive an "S" stamp when it is complete. Sorry about the quality of the photo - camera phone.
Monday, April 8, 2013
Spring!
I throw open the shop doors! I thought it would never get here. Now things can cure without heat lamps and what not.
I glued in No. 1 bulkhead this past Saturday morning.
Here's the view from the front. The little block in front of the feedwater tank supports is a mast step. Why a mast step? I don't know, some day I may want to add a fore mast. How else would one rig ship for holidays, etc.? I'll sand the fillets after they fully cure and blend the paint.
I glued in No. 1 bulkhead this past Saturday morning.
Here's the view from the front. The little block in front of the feedwater tank supports is a mast step. Why a mast step? I don't know, some day I may want to add a fore mast. How else would one rig ship for holidays, etc.? I'll sand the fillets after they fully cure and blend the paint.
Tuesday, April 2, 2013
Interior Painting & Sanding
Painting and sanding all of the parts that one won't see. But it's all about protecting the composite finish and making it easier to clean. This picture was taken with my phone camera, so the lines are a little distorted. One can see the first coats of Grand Banks Beige in the counter stern and extending forward from bulkhead No. 5. Bulkhead No. 1 still isn't glued in yet as I finish up things in the forepeak that would be more difficult to do later.
Tuesday, March 12, 2013
Thursday, March 7, 2013
British Engineering
My dream marine compound ...
I don't have this one, but I did obtain her little sister, Mills - Beaumaris No. 5
I don't have this one, but I did obtain her little sister, Mills - Beaumaris No. 5
Sanding, Fairing, 'Glass and then, Paint!
A plywood hull offers vast smooth expanses, but where it is joined or scarfed requires much fairing, smoothing and disguising the "boxy" reputation. The stem, ready for fiberglass cloth ...
I realized I didn't take any pictures of the 'glassing process. I was way too busy building up consecutive "green" coats to fill the weave of the cloth. Started at 0600 and finished by 2300. But after fairing that, epoxy primer followed.
A view aft, between coats ...
I realized I didn't take any pictures of the 'glassing process. I was way too busy building up consecutive "green" coats to fill the weave of the cloth. Started at 0600 and finished by 2300. But after fairing that, epoxy primer followed.
A view aft, between coats ...
The Stern Tube
A professional builder would have incorporated the stern tube in the keel structure. However, I was in exploratory mode, not knowing what engine I would have or what size propeller shaft I would need. So I bored it retro ...
There, the deed is done - a veritable owl's nest.
We check the fit and then fair in a surrogate of the stern tube without bonding it in yet.
Wax paper is our friend. Even so, after fairing, I had to whack the surrogate out with a mallet. Epoxy is a fearful thing.
There, the deed is done - a veritable owl's nest.
We check the fit and then fair in a surrogate of the stern tube without bonding it in yet.
Wax paper is our friend. Even so, after fairing, I had to whack the surrogate out with a mallet. Epoxy is a fearful thing.
Planking Complete
The box keel is planked and fairing begins in earnest. The box keel is an old design, dating from the first half of the 19th Century, appearing on the Jersey Shore in Sea Isle skiffs and other craft. It's advantage is greater space and buoyancy than deadwood, with the opportunity for a true bilge sump.
Midsummer's Progress
Here's a view of the bottom planking moving aft, how it is rounded at the chine and how it is scarfed in place.
Starting the stem laminations in this next shot and fairing the bottom planking.
Starting the stem laminations in this next shot and fairing the bottom planking.
Wednesday, March 6, 2013
Stern Redux
The planking around the stern was laminated in four layers of 0.125":
And now finally, the lines of the classic Victorian launch, albeit in modern wood materials, begins to appear:
And now finally, the lines of the classic Victorian launch, albeit in modern wood materials, begins to appear:
Compounding Plywood
Plywood, as it turns out, is not fond of being compounded - that is, being twisted in more than one plane. But it is possible. In this bow-on view, 0.250" marine ply is twisted through @ eighty degrees while at the same time conforming to the curve of the bottom:
After the 0.250" layer, a 0.375" layer will be laminated on, overlapping the seams. Here's another view of the planking as of Spring 2011:
After the 0.250" layer, a 0.375" layer will be laminated on, overlapping the seams. Here's another view of the planking as of Spring 2011:
Tuesday, March 5, 2013
Stern Structure
Winter of 2010 is setting in as a jig is set up to receive the aft keel timber. One can see how I've been busy with the planer elsewhere as the sides and bottom are ready to receive planks.
And here's the stern knee and keel timber bonded to the bottom of the box keel.
And here's the stern knee and keel timber bonded to the bottom of the box keel.
Stern Curves Part II
The stern frames are fitted, expoxied to their station and fitted and epoxied to the chine logs and sheer clamps. The frame member in the center is being laminated prior to planing.
That Elliptical Stern ...
Reuel specifies laminated stern frames to create the curvy elliptical stern that is the hallmark of a turn-of-the-last-century launch. In a blur, somehow all of this will come together.
And it does ...
And it does ...
Fitting to the Stem
The chine logs are screwed in and bonded with thickened epoxy. I'm fitting and springing in the sheer clamps with a ratchet strap.
Subscribe to:
Posts (Atom)